welding holes in thin sheet metal Now that we’ve covered the essential considerations for different arc welding processes, let’s discuss how to prevent and fix common . See more To install this type of clamp, insert the threaded end into a knockout hole in the .
0 · welding 24 gauge sheet metal
1 · welding 22 gauge sheet metal
2 · welding 16 gauge sheet metal
3 · welding 14 gauge sheet metal
4 · tig welding thin sheet metal
5 · tig welding stainless sheet metal
6 · tig welding sheet metal videos
7 · mig welding sheet metal basics
Section 406.9(B)(2)(a) applies to receptacles installed in a wet location where the product intended to be plugged into it is not attended while in use, so it must have a weatherproof enclosure with the attachment plug cap inserted or removed.
Each welding process requires specific precautions and equipment setup for a successful sheet metal weld. So, let’s discuss the preparation needed for each arc welding process before proceeding to the common problems with thin gauge welds. See moreNow that we’ve covered the essential considerations for different arc welding processes, let’s discuss how to prevent and fix common . See moreWelding thin metal is challenging. There is no denying that. But, if you practice and use the tips we shared in this article, you’ll get the best chance for success. After you inevitably burn through some scrap sheets of metal and warp others, you’ll gain more experience and learn . See more To weld thin metal, choose an appropriate process (TIG or MIG with low amperage), use a smaller diameter wire or filler rod, and adjust travel speed to prevent burn-through. Employ a pulsing technique, stitch welding, or .
Welding holes in thin metal or sheet metal is a crucial skill. Whether you're correcting a mistake or shaving a body so it's perfectly smooth this skill will. In this video I demonstrate how to set up your mig welder so you can weld thin sheet metal. We also showed in this video how to make your pattern, fit and weld it in. I demonstrated this. What’s the Best Method of Welding Thin Metal? When it comes to welding slimmer metal sheets, MIG and TIG are the best option. The two work perfectly on nearly all material types. Nonetheless, if your aluminum or .
Welding thin sheet metal requires patience, precision, and an understanding of the material properties. We are proud to have mastered these challenges at Shengen and pushed the . This article covers everything you need to know about welding thin sheet metal: from tips for beginners to advanced welding techniques that experienced professionals use under difficult circumstances. In this video I show how to fill holes in sheet metal using a mig welder. This is always challenging do to the thin sheet metal cars are built out of today.
welding 24 gauge sheet metal
MIG welding sheet metal. When welding thin metal, the main objective is to avoid warping, burn-through and excessive heat-affected zones while still ensuring the weld has enough mechanical strength for the application. The most common processes for thin metal welding are TIG (Tungsten Inert Gas) and MIG (Metal Inert Gas). TIG welding is ideal for thin metals as it offers precise control over the heat input, which is essential for .This method helps to avoid burning and making holes in the thin metal sheet. For a better result, you can adopt the padding method. Most of the welder burns the rod down on the top of the material. But they do it in straight lines. . you may .
The filler metal is the material that melts into the weld and fills the gap between the two pieces being joined. MIG welding simplifies the feeding of filler metal, making the welder’s job easier. While the specific material may not .In this article, we present crucial tips for welding thin metal, exploring the unique challenges of welding thin metal, and providing practical tips to help you overcome them. These tips are designed to guide and support you in your .
ace junction box
What welding rod to use for thin or sheet metal? The E6013 welding rod is the best to stick weld thin mild steel and is known as a sheet metal rod. An E6013 has a flux covering with high amounts of rutile. Rutile creates the smoothest arc with light penetration that won’t burn through the joint as easily as other rods. An E6013 is very easy . Yesterday I was welding some exhaust tubing and had trouble blowing holes in the material. Welder set to MIN and speed anywhere between 6-9. . I am trying to still get some feedback about the best wire for my machine to use with thinner sheet metal. . I don't do a whole lot of welding, and even less on thin metal so getting a much more . The quest for seamless body repairs eludes many DIYers when they face the menace of welder blow-through. The problem occurs when a weld penetrates completely through the material, either leaving a hole or enlarging the weld area. This is a common issue, especially when welding thin materials like patch panels or other forms of sheet metal. In this video I demonstrate how to set up your mig welder so you can weld thin sheet metal. We also showed in this video how to make your pattern, fit and we.
Here is exactly how to weld without burning holes: Before you begin welding, read the company guidelines listed on the electrode packaging, the specifications included with your welder, and know the thickness and type of the metal you are welding. You need the correct amperage, the ideal electrode for the base metals, and proper techniques to . The problem with welding sheet metal or thin gauge steel is that you can easily blow holes in the panel and create a big mess quickly. . Quick Welds-When welding sheet metal with a MIG welder you do NOT want to try and run one long bead like when you’re welding heavier metal. Sheet metal warps easily and also can burn through easily . Thinner wire does help greatly. Depending on guage 0.030 wire can do sheet metal, 0.024 will do it better with more precision. Welding sheet is a whole different animal from say plate, you dont have to build heat into the pieces and let the weld flow, its more keeping the heat down and not burning through what you are trying to join.
In this video I show how to fill holes in sheet metal using a mig welder. This is always challenging do to the thin sheet metal cars are built out of today. .
In this video I share the easy way to fix small holes in sheet metal with a mig welder. This mig welding process works well with rust repair also. The trick .Stick welding is not the preferred method of welding thin sheet metals but if you have no other option then it can be done. The first thing you need to keep in mind is to select a thin electrode and work on a low amperage. Rods like the 7018 and 6013 are preferred. . You can also try padding to avoid making holes in the base metal.Welding thin sheet metal requires patience, precision, and an understanding of the material properties. We are proud to have mastered these challenges at Shengen and pushed the limits of sheet metal fabrication. . How to fix mistakes in thin metal welding? Fill in holes with minimal heat and grinding. Controlling heat and cooling can . Things to Consider When Welding Thin Metal. Welding thin metal can be a challenging task, but with the right techniques and considerations, it can be done successfully. Here are some important things to keep in mind when .
In this video I show how to set up and tig weld thin metal. There are a lot of different steps to take and I try to make it as easy as possible. From how to . Using Flux Core Welding for Thin Sheet Metal. If you have ever attempted to weld thin metal, you are probably aware that welding this kind of metal is extremely difficult. Weld metal that is less than 6mm will have a .
There are some tricks to welding thin sheet metal.Proper welder setup is critical. We are using a Millermatic 211 AutoSet MIG welder with .023 wire. The thinner wire is best for sheet metal. Because we are using an extension cord (240v), we adjusted the AutoSet wire setting to .030 wire. The weld initially looks bad because of the slag from flux core welding. Spatter. Tiny beads of metal also get left behind after flux core welding which can create more grinding work. Porosity. You’ll get tiny holes or pockets of contamination in your weld. Blow out. This is when your sheet metal literally blows out the sheet metal into .
This video is a tutorial on welding thin metal with the UNIMIG VIPER 185Email: [email protected]
Skip Welding Technique. When welding thin sheet metal, do not try to run one bead right across the joint. This will cause too much heat to build up. Instead, run a series of short welds at different points in the metal that eventually join together. Leave the metal to cool for a second or two between welds to help the heat dissipate.
ok, im not a professionally welder lol. My little mig welder has left a few pin holes in my sheet metal repair. What is good to fill these in with before laying filler over it? I've heard bondo glass is good, and I've heard just seam sealer will work. I don't want the filler to start bubbling a few years down the road. thanks Mig Welding Thin Sheet Metal. Mig welding is a popular and straightforward method of welding thin sheet metal. For mig welding, you don’t need much in the way of equipment. You will only need a mig welder and a proper technique for mig welding thin metal. If you are new to welding, start by welding with a low-amperage setting and a small wire . I keep blowing through my thin sheet! Andy gives helpful insights and tips to MIG weld thin sheet metal.KINGMETALS.com
welding 22 gauge sheet metal
Can You Weld 22-Gauge Sheet Metal? You can weld a 22-gauge (0.03-inches) metal sheet using a TIG welder or even with a MIG welding unit. However, it is not recommended to stick weld 22-gauge sheet metal as excessive penetration is highly likely to occur and become problematic. The 16 gauge or 1.5mm is a safe bottom limit for material thickness .
Today we will be going over some tricks to weld thin gauge sheet metal like body panels while avoiding wrapage. I go over 2 different techniques and several . Techniques for MIG welding thin sheet metal. MIG welding thin sheet metal requires specific techniques to ensure a successful weld. Here are some tips to help you achieve high-quality welds: Maintain a short arc length: Keep the arc length as short as possible without touching the metal. A shorter arc length helps to minimize heat input and .
ace hardware mailbox mounting bracket
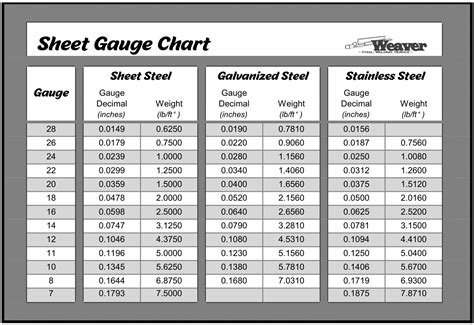
acme sheet metals inc
The existing wires (old BX, some going back to the late 1920s, some to the 1960s) are almost certainly too short to work in a new 200A box. If I don't use the old box as a junction box, I'd just have to mount another large junction box (or several smaller ones) in its place.
welding holes in thin sheet metal|mig welding sheet metal basics